The Final Fulcrum Pin Fix!
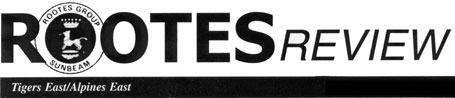
An Article by John Logan
October , 2001
From the 5/97 Rootes Review with corrections made on 10/14/01.
Page 1
Several people have asked for more information on the fulcrum pin reinforcement that that they have seen on my Tiger and that I briefly described during the technical session at the 1996 Orlando United XVIII.
Why should we be concerned?
There has been a lot written about the weaknesses in the basic design of the front suspension of the Alpine and Tiger as well as some of the after market fulcrum pins, so I wont go into the reasons again why you should be concerned. However, I will add one more condition that I havent heard much mention of.
Here in Michigan we have the high damaging loads from broken roads and potholes. Some of you that attended United XVII commented on the condition of our roads and that was after our spring repair.
In the winter of 95, a deer got trapped in a pothole near Detroit. After getting hit, flattened by passing cars and frozen, a patching crew came by and covered him up. When spring came of course he began to swell and blew the patch out for all to see. You may have read in your papers about the lawsuits that followed. Well so much for why!
What is the modification?
Im going to describe only an improvement to the fulcrum pin and its attachment to the front crossmember, since there are many adequate solutions to the other front suspension problems.
The modification consists of a 1" square structural tube running parallel to each fulcrum pin that is welded to the bottom face of the crossmember. Each end of the tubes are connected with links to each end of the Fulcrum Pins.
Why does it work?
Because of the relative stiffness of the added tube, approximately 75% of the loads that are generated from braking, cornering and wheel impacts are transferred directly to the tube through the links.
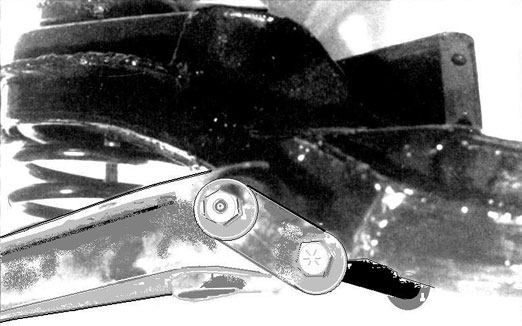
Loads are transferred directly to the tube through the links.
Thus the stress that can causes fatigue failure of the fulcrum pin, the four small attaching bolts and the welded tapping blocks is reduced by 75%. Those of you familiar with the laws of material fatigue will recognize that, considering previous failure history, the redesign should provide infinite fatigue life of the assembly.
This redesign also provides a redundancy by being able to support the lower control arm in the event of an accident. I realize this is not an easy job, but it eliminates a lot of worry when you or your loved ones drive your car hard or long way from home.