Joe Parlanti
B382000026
Seat Bottoms
At this point you should have everything off of the frame and it’s time
to clean them up and repaint. The easiest thing to do is to sandblast
them. I personally prefer powder coating over paint which requires a
bare metal surface so that’s what I did. I use the Eastwood system to
powder coat everything I can and all of the seat parts were finished in
this manner. Here are a couple shots of the completed frames: (The
color is a little dark because I used powder I already had instead of
buying something closer to original)
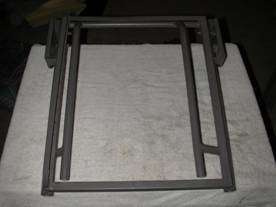
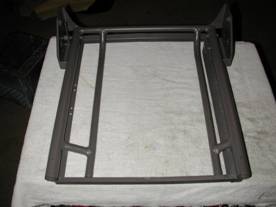
At this point it’s important to identify the type of seat that you
have. There are basically 2 types that were used in the Tiger which
I’ll call "early" and "late". An easy, but unreliable method to
determine which type you have is to look at the covers themselves. The
early seats have 7 pleats on the seatbacks while the later type has 12.
However, as we’ll see later in the article, it’s easy to mix and match
the various seat types and cover styles. The early and late seat
bottoms use entirely different cushion suspension techniques and are
specific to the frames themselves. The early seats use a series of
rubber straps and canvas to support the foam cushions, while the later
seats use a rubber diaphragm which hooks directly to the frames. I had
originally thought that my seats were the later type based on the fact
that my car is a Mk1A and that I had found remnants of a diaphragm
under the cushions, even though there were the homemade straps as
previously discussed. Having these clues, I ordered the parts to do a
later type seat only to find there was absolutely no way the diaphragm
would fit on the frame. After talking with Rick at Sunbeam Specialties
and Martha Wheat, I found that some early Mk1As like mine (B382000026)
were fitted with the earlier type seats so I sent back the diaphragm
kits and ordered the straps. The earlier seats also use a set of 4
canvas pieces to provide attachment points for the straps. Martha said
that all of the foam cushions were the same for either seat type and
that the later covers would work on the earlier frames. I like the look
of the later covers so I opted to keep them.
The first step in reassembling the seat bottoms is to assemble all of
the parts. Here’s a shot of the various pieces needed to get started:
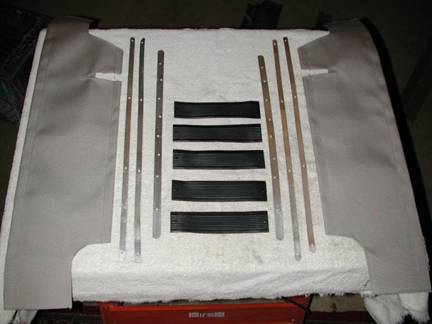
Begin by threading the canvas pieces through the seat frame in the
same manner as the ones which were removed, inserting 2 of the thinner
straps into the pockets in the canvas. Using an awl, push through the
canvas and the 2 metal strips to locate the corresponding holes in the
seat frame. Once you are satisfied that everything is lined up, pop
rivet in 4 places using 1/8" rivets. At this point the seats should
look like this:
Dscn2670.jpg
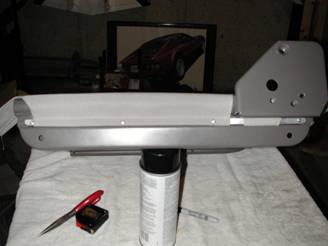
It’s now time to install the rubber straps. There are 6 straps in
all, five short ones and a long one. Insert a seat hook in each end.
Since my seats were missing the hooks I acquired a set from Martha
Wheat. Here are some photos of the straps and hook detail in case you
need to make your own:
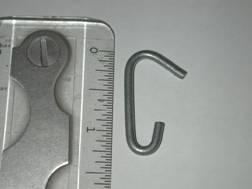
The long strap attaches directly to the longitudinal tubes in the
seat frame as shown here (canvas removed for clarity):
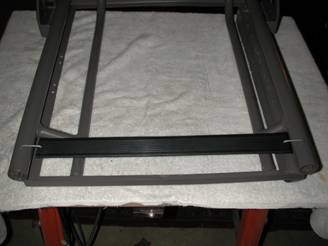
Next we’ll install the thick metal strips into the canvas supports.
It’s important to position these strips properly to ensure equidistant
placement of the straps. Begin by laying the strip over the pocket and
marking where the end would be to position the first hole 5" from the
rear of the canvas. Note: the distance to the first hole is different
from each end of the strip. The longer gap goes toward the front of the
seat. Here are a couple of good shots showing the installation of the
strip:
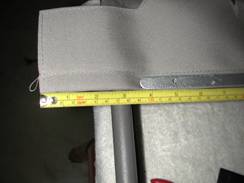
Once the strips are in place attach the 5 short straps with the
smooth part of the straps on top. At this point your seat will look
like this:
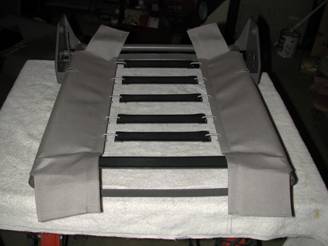
The seats have a very unique item used to support the front of the
foam cushion. It’s actually made from bungee cord material and mine was
beyond hope, so I had to make a new one. Here’s the process I used:
The first step is to recreate the wooden plugs which go in the
longitudinal tubes. I used a 1" dia. dowel cut to the appropriate
length (1.5"). Lightly sand and bevel the edges. Next drill a 13/32"
hole through the dowel (you may need a larger hole depending on the
bungee used). Here’s a shot of the dowels:
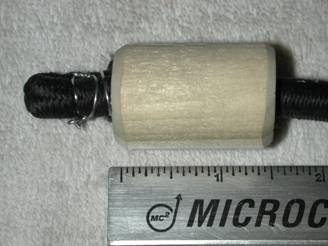
I cut the bungee cord to the appropriate length leaving one end
untouched. I found that 16" between the dowels works fine and keeps it
taught when inserted into the tubes. Slide the hook off of the free
end. No sense in having to tie up both ends.
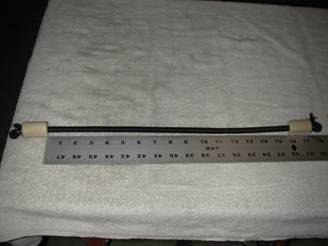
I used safety wire to tie up the free end. Double it over and then
twist the wire to secure the loop. None of this is critical, but it’s
better to err on the side of making the bungee too short than too long.
Here’s a detail shot of the end:
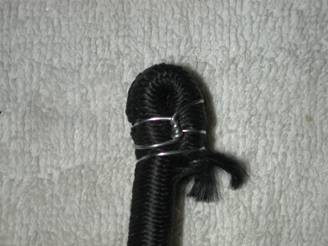
Now you are ready to insert the dowels into the tubes. Make sure
that the tubes are not dented or there is weld material on the inside
or it’ll be difficult to drive the dowel in. I found that they fit
snugly without any adhesive using a small hammer to push the dowels in.
Here are a couple of shots showing the end detail and the finished
bungee in place:
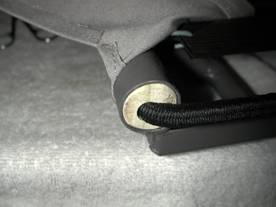
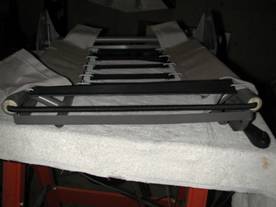
Once the bungee is in place the front flaps of the canvas supports
can be wrapped around the bungee and secured. Martha suggests stapling
them in place, but I couldn’t figure out how to get the stapler over
the canvas. On the first set I sewed them together but glued them on
the second. Either way seemed to work fine. Here’s a view of this step:
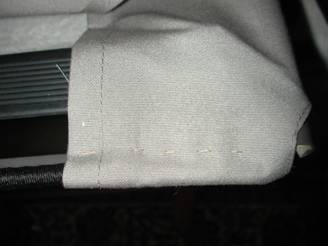
The rear flap is glued in place as shown in this photo:
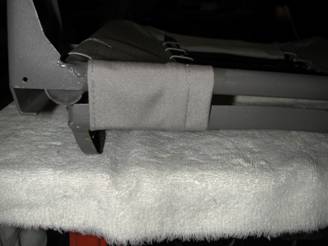
Now’s a good time to talk about adhesives. Martha suggests contact
cement. She uses a commercial product purchased in quantity but said
that it’s the same as can be purchased at a local hardware store. I
actually tried a couple of different things including a spray contact
adhesive made by 3M and available at auto parts stores. There are 2
types of the 3M glue and the one I used was labeled Super Trim Adhesive
with a part number of 08090. It’s supposed to be stronger and handle
heat better than the one with 08080 part number. It worked reasonably
well but I liked the control I had using the brush type contact
adhesive. I used Weldwood contact cement and then also tried a new
version of the same adhesive in a gel form. The gel type didn’t go as
far but I felt like it penetrated better. The key with the Weldwood
stuff is to stay away from the odorless, water-based versions and go
for the full out nasty, volatile types. Just make sure you heed the
warnings on the can. I used at least 2 coats, and normally 3, on each
part to be joined. Wait about 20 minutes and join the 2 parts together.
Firm pressure will set things quickly. Full strength is achieved in 24
hours.
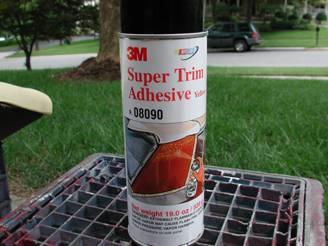
The 3rd piece of canvas can now be installed. It has a
pocket through which the 1st
short rubber strap is inserted. Unhook the strap and feed it through
the canvas. Center everything up and glue to the front to the frame
wrapping it around the bungee as shown here:
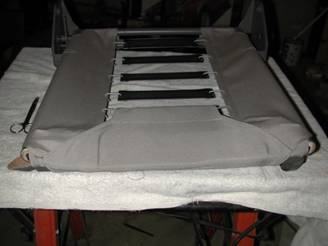
Now for the final step in the seat cushion suspension procedure.
Take the last piece of canvas which is rectangular with no sewn edges.
Position it over the top of the straps and other canvas pieces and glue
as shown here:

The bottom will look like this after all the canvas is glued in
place:
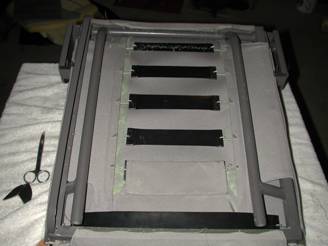
One tip that Martha suggested was to tuck a small piece of cardboard
into the canvas on the front of the seat frame to protect the vinyl
cover from the edge of the longitudinal tubes. Martha actually sent me
these cardboard pieces which work fine but the outlines are noticeable
through the vinyl cover. Here’s how it looks in place on one of the
corners.
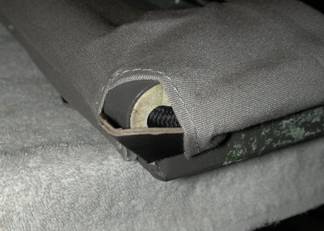
The cushion is glued down using contact cement. Use liberal amounts
all over the canvas and the front and rear metal supports. It’ll look
like this when you’re done.
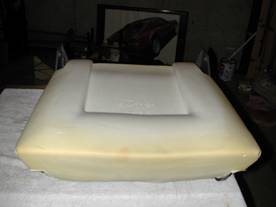
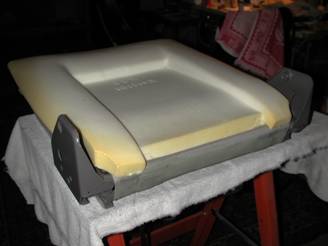
Now we’re finally ready to install the covers. The most important
part of this procedure is where to apply the glue. It’s critical to
glue the center of the seat cover to the foam. Only the first 1.5" of
the perimeter needs glue as shown in these photos:
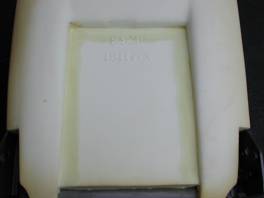
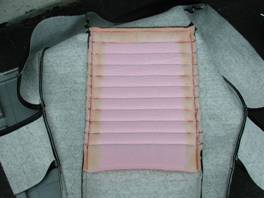
Once the glue has been applied to these parts, put it away as you
won’t need it any longer on the seat bottoms. Position the center of
the cover over the foam paying particular attention to line everything
up. After I glued the center down, I waited until the next day before
the next step to let the glue cure fully.
There are 24 clips used to secure the vinyl cover to the frame but
hold on to them until the final stretching. A good tip is to put the
seat bottom in the sun for a half hour or so to make the vinyl more
pliable. A good tip I heard from a TE/AE member at this year’s United
was to put the vinyl cover in the drier for a couple of minutes to
soften it up. I went through a couple iterations of stretching and
clipping the vinyl. I used medium sized binder clips which can be
removed easily as you stretch the fabric. Here’s a shot of the binder
clips:
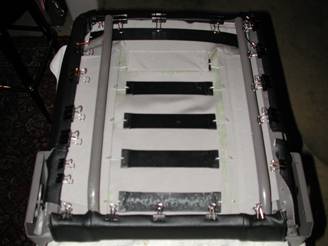
Once you’re satisfied with the fit of the cover, tap the original
clips on with a tack hammer and you’ll be half way there!
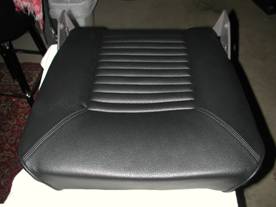
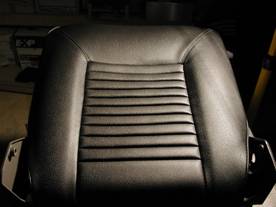